Linbrooke Services discusses how it delivers outstanding improvements to the railways with minimal disruption to clients, the passengers they serve or the environment.
Multidisciplinary engineering company Linbrooke Services Ltd has installed innovative new quick deploy location case stagings at Flitwick and Harpenden stations, completing work in just two ‘Rules of the Route’ shifts, and without on-track plant or overhead line isolations.
Ambitious life extension programme
Linbrooke delivers connectivity and technology integration solutions, serving customers in the rail, utilities, and global subsea sectors. An approved Network Rail tier one Principal Contractor, it developed the industry-first stagings as part of its four-year West Hampstead Life Extension Programme.
Launched in 2020, the programme will see Linbrooke upgrade signalling assets in 12 interlocking areas, life-extending them for a minimum of 10 years. Following initial interventions at Cricklewood and Tottenham North Curve, Project Director Scott Louder organised collaboration workshops, which resulted in the development of the up and down bank stagings.
Scott Louder, Project Director, Linbrooke Services Ltd said: “Taking lessons learned from the first two interventions, it was agreed that the remaining 12 interlocking interventions would be a journey of self-delivery and innovation, and one of those innovations was certainly a game changer.”
A staging solution that saves time and money
Working with Network Rail and its supply chain, Linbrooke developed modular up and down bank staging platforms with screw anchor piles. These piles meant that, unlike traditional platforms, the stagings could be installed without on-track plant, holes, concrete, or water.
As a result, works would have virtually no environmental impact, would not require OLE isolations, and could be completed in just two shifts – a 60% reduction in installation time.
“As demonstrated, there is a huge time saving on installation when compared against traditional down bank staging solutions,” added Scott.
In addition to delivering time and cost savings, the UK-made stagings can strengthen embankments, which helps to prevent landslides.
Unlike traditional fixed platforms, they can also be removed, relocated, and redeployed.
Finally, their legs are used as earth points for the signalling location case, making them a highly innovative, multi-purpose solution.
Scott and his team installed eight down bank stagings at Flitwick and eight at Harpenden including one upbank staging (featuring steps). They hope to roll out their new design further as the life extension programme continues.
A demo staging was also installed at Linbrooke’s London project office, inviting stakeholders to view and test it.
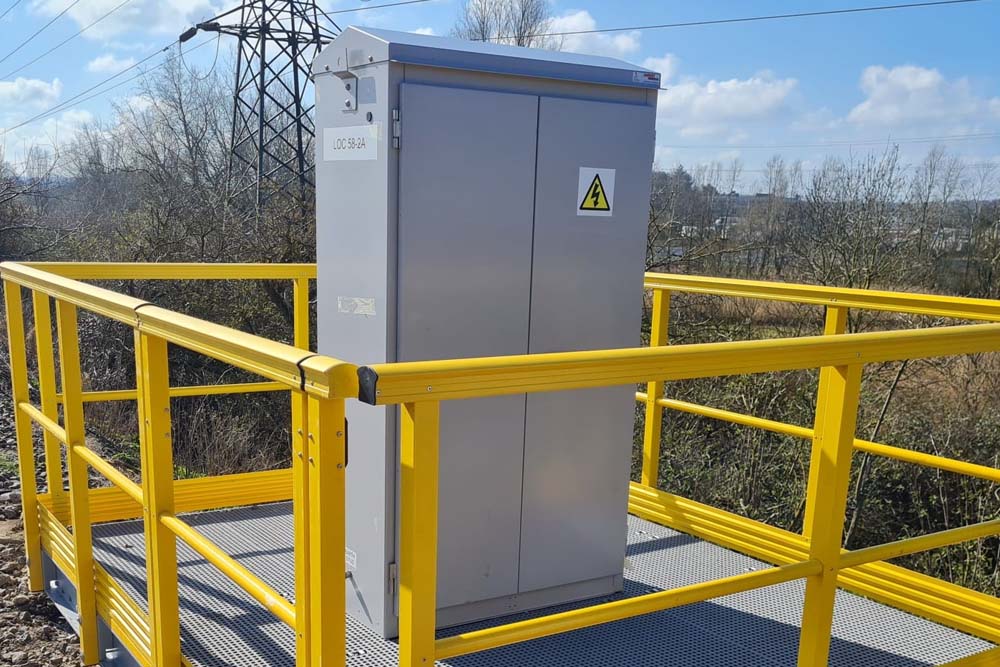
Doing things differently
The innovation reflects Linbrooke’s broader mission to challenge accepted practices and provide alternative solutions. Scott attributed the project’s success to a supportive working environment, where collaboration, sustainable development, expression, and free thinking are encouraged.
Delivering the best return on investment and striving to achieve net zero are also guiding principles for Linbrooke.
Reflecting on the project’s environmental and cost implications, Scott added: “The team have worked diligently and professionally, from design to delivery. They’ve created a solution that leaves virtually zero environmental impact, as this revolutionary system is all installed with hand-driven plant, requires no OLE isolations, no on-track plant, and zero water or concrete, achieving maximum value for each pound in the ground.”